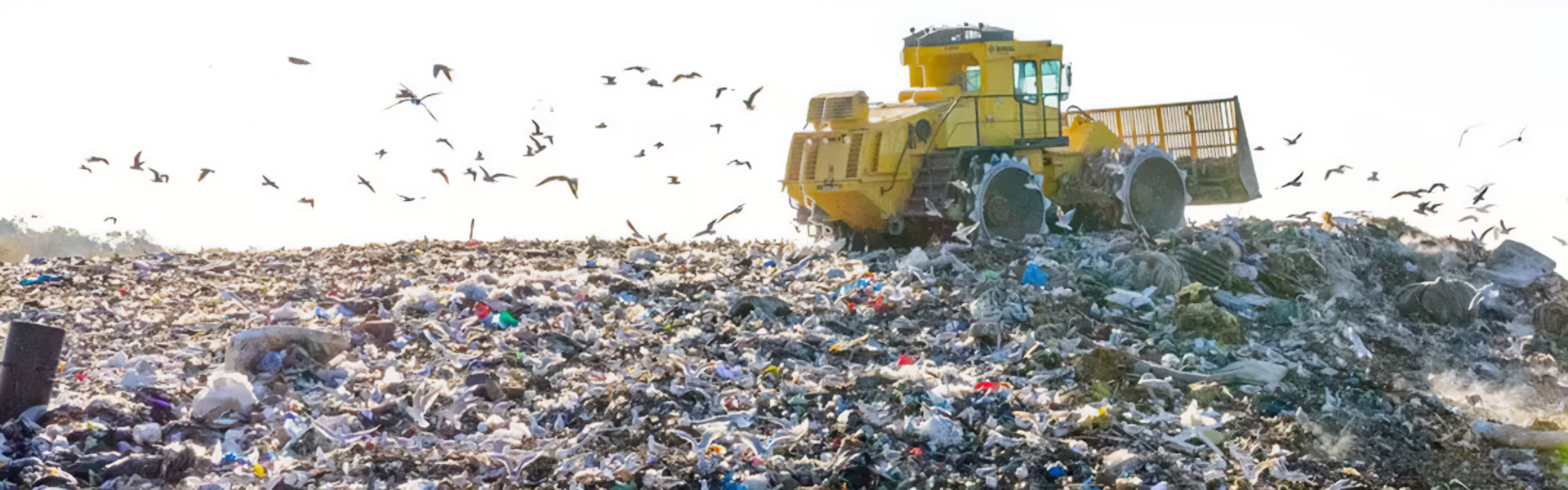
Landfill gas
a by-product of waste management
Recovering landfill gas (LFG) to produce renewable natural gas (RNG), also known as “biomethane”, is a challenge in terms of technology and cost: the flow rate and composition of the gas are unpredictable and vary all the time. Expert knowledge of LFG is key to making an injection project a success.
Three types of gas in varying proportions
LFG is a mix of three gases in varying proportions: biogas, generated by the decomposition of organic matter contained in the waste; air, which infiltrates into the collection network; and various volatile organic compounds produced by the waste.
1) The biogas produced spontaneously by the decomposition of organic matter
Landfilled waste contains a significant amount of organic matter, in the form of food waste, green waste, paper, cardboard, leather, wood, etc. It represents about 50% of overall tonnage and still 25% when waste is sorted upstream.
Inside the cells, the organic matter is degraded by various microorganisms which thrive in humid and oxygen-deprived environments. The most active micro-organisms are so-called methanogenic bacteria, which produce methane (CH4) as a metabolic by-product in hypoxic conditions.
This spontaneous phenomenon produces a biogas consisting primarily of methane and carbon dioxide (CO2). It also contains traces of hydrogen sulfide (H2S), ammonia (NH4), hydrogen (H2), organic sulfur compounds (called mercaptans) and various acid gases or aerosols.
The proportion of each of these components varies over time as the organic matter passes through different degradation stages.
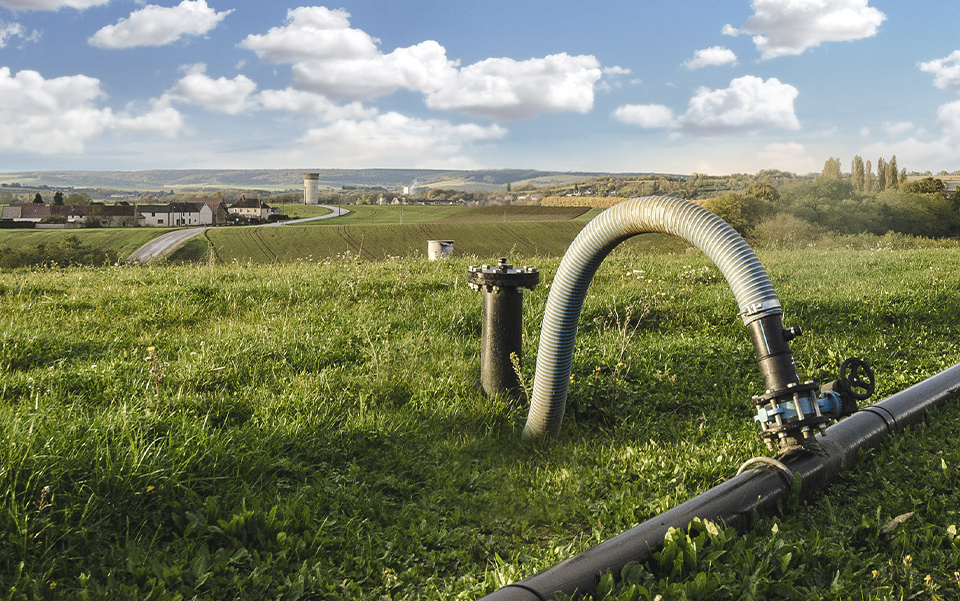
2) The air entering the collection network
Methane is a highly flammable gas. It is also a greenhouse gas with a global warming potential 20 times larger than that of carbon dioxide. Landfill site operators have to collect this gas to prevent fire and explosions, but also to avoid direct emissions into the atmosphere. Collection is also a way of reducing odor nuisance (caused primarily by hydrogen sulfide and ammonia) and helping to regreen the site.
A standard LFG collection system consists of a blower hooked up to a network of wells, installed vertically and/or horizontally in the waste mass, which transport the gas to a flare stack or an energy recovery unit. Given that such networks are never completely airtight, they also draw in air (oxygen and nitrogen). The volume of air present in the LFG depends on various factors, such as blower settings, cell wall permeability and the airtightness of conduits.
3) Volatile organic compounds (VOCs)
The collection network also draws in volatile compounds produced by waste such as paint, solvents, detergents, etc. These compounds include hydrocarbons, siloxanes, aerosols, dust, particles and volatile metal compounds. The various trace compounds are grouped together under the term “volatile organic compounds” (VOCs).
The chemical composition of LFG
The gas arriving at the flare stack or the energy recovery unit is a mixture of biogas, air and VOCs. It consists of methane (CH4), carbon dioxide (CO2), oxygen (O2) and nitrogen (N2), as well as various trace compounds. The proportion of each gas varies from one site to another – it depends on the type of waste landfilled, the degradation phase and other external factors.
The blower settings influence the volume of air in the LFG directly. The stronger the pull, the more air infiltrates through imperfections in the collection system. The weather conditions play an important role too: a high level of humidity combined with warm temperatures stimulates bacterial activity and biogas production. Variations in atmospheric pressure also have a direct impact on the level of oxygen present in the LFG.
Methane (CH4)
LFG gas contains 40 to 50% methane (CH4) on average. Methane is an energy-rich gas – it is the main component of fossil gas, which we use for heating and transport.
The solution commonly used to recover methane from LFG is to burn it in a turbine to generate electricity. But the energy yield is low. WAGABOX® technology makes it possible to separate the methane from the other constituents so that it can be injected directly into the natural gas grid as a substitute for fossil gas.
Carbon dioxide (CO2)
The carbon molecules found in LFG, in the form of carbon dioxide (CO2) or methane (CH4), come from the degradation of organic matter. The molecules were originally absorbed by living organisms as they grew (via photosynthesis), and find their way back into the atmosphere during degradation. Therefore, this organic carbon does not actually increase the quantity of carbon present in the atmosphere (short carbon cycle), whereas the carbon emitted by burning fossil fuels does.
As for non-biodegradable carbon contained in synthetic organic materials such as plastics, it remains trapped in the ground. A landfill site therefore acts as a “carbon sink”, or in other words, a reservoir that contributes to reducing the quantity of carbon in the atmosphere.
Oxygen and nitrogen (O2 and N2)
LFG includes 10 to 30% air. A high concentration of air makes methane separation much more difficult: filter technologies are ineffective as methane, oxygen and nitrogen molecules are roughly the same size, and methane and oxygen can be explosive when mixed in certain proportions.
WAGABOX® technology uses cryogenics to separate the methane from the air gases. This breakthrough technology guarantees a high quality RNG (biomethane) that can be injected directly into natural gas grids, regardless of the levels of oxygen and nitrogen in the LFG.
Hydrogen sulfide (H2S)
Hydrogen sulfide (H2S) is a highly toxic and corrosive gas, with the characteristic foul odor of “rotten eggs”. It attacks steel and copper, and has to be removed before starting the energy recovery process, to prevent equipment from being damaged.
The concentration of hydrogen sulfide and other sulfur compounds (mercaptans) in LFG tends to be higher in landfills that receive industrial waste with a high sulfur content, such as drywall used in construction. At some sites, concentration levels can reach 10,000 ppm at times (Waga Energy measurements).
Sulfur compounds are a risk factor for personnel, a source of odor nuisance for local residents, and an extra cost that needs to be budgeted when setting up an energy recovery project.
A production rate which fluctuates over time
LFG production takes place over several decades. It regularly increases when the site is in operation, and peaks a few months after the last load of waste has been landfilled. It then gradually declines until all the organic matter has been degraded.
Optimizing energy recovery at an landfill gas extraction site
Gas production at a landfill site can be partly controlled by regulating the LFG collection system and adjusting blower settings in particular. There are two possible approaches:
- Operating the network in “depollution” mode
The blower draws in the LFG at a high rate and maintains the vacuum in the landfill at a high level. It helps to reduce odor nuisance but can increase the concentration of air up to 30%.
- Operating the network in “recovery” mode
The blower keeps the vacuum at a constant, low level. If the valves are precisely controlled and the LFG collection network is sufficiently airtight, the air content can be kept to below 15%.
A landfill site operator often has to combine the different settings according to the production level of the different cells and the various, sometimes conflicting, constraints: methane recovery, odor nuisance reduction, polluting emission reduction, etc.
Managing bioreactor landfills
This technology surfaced in the US during the 1990s. The goal of bioreactor landfills is to speed up organic matter degradation and stabilize waste by enclosing it in a confined chamber and irrigating it with landfill run-off water, or so-called leachate. This system stimulates microbial activity while also diluting any inhibitors (ammonia, salts, sulfur, etc.). When the cell is covered with an airtight membrane, a bioreactor needs to be installed to enable the organic matter to decompose and prevent the waste from becoming “mummified”.
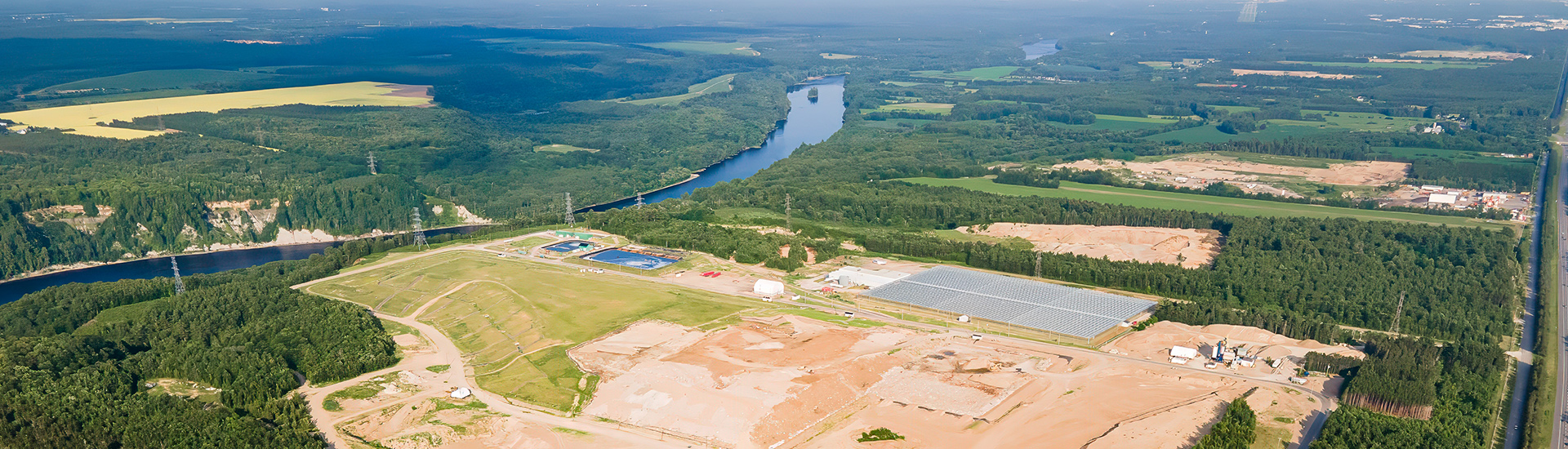