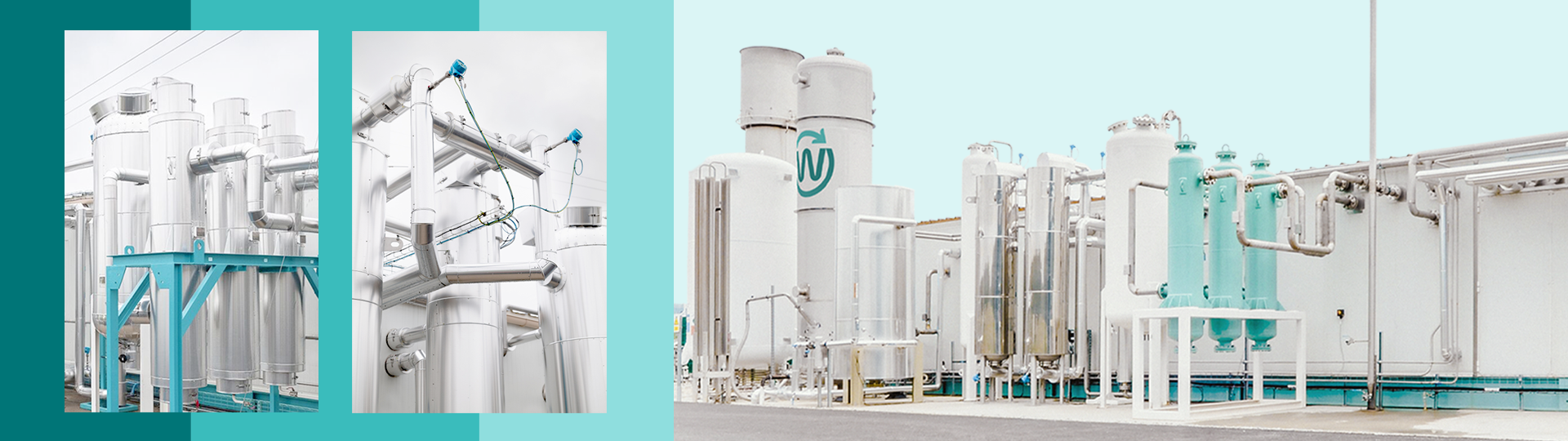
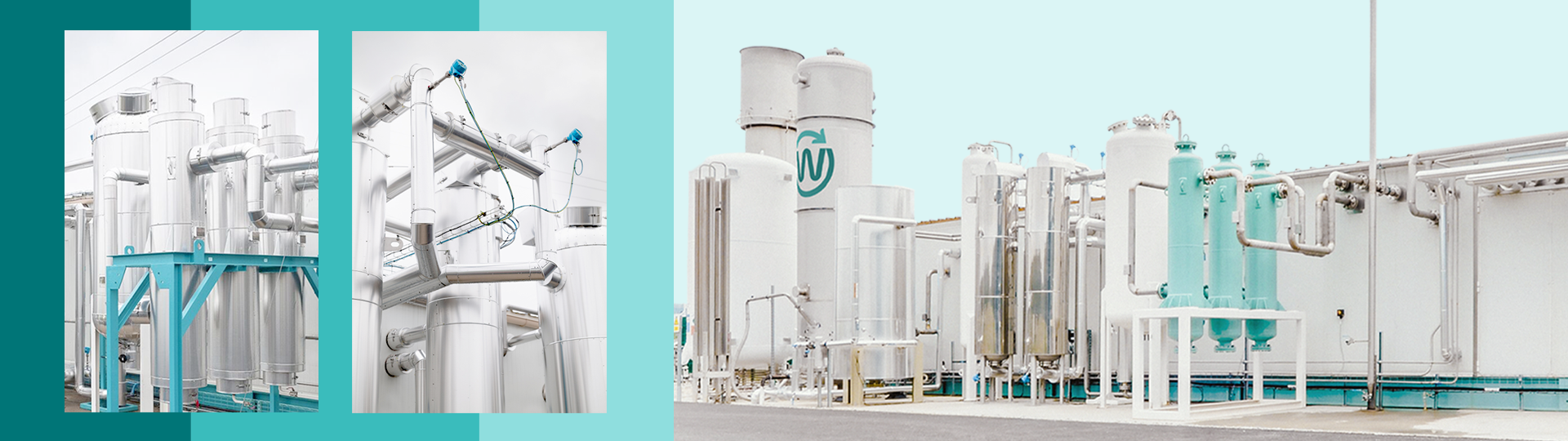
Discover how a WAGABOX® unit works
Visit to the WAGABOX® unit at the Suez site in Les Ventes-de-Bourse (Orne)
Detailed information
Waste is stored in chambers lined with an airtight geotextile membrane. Once full, they are covered with another membrane to seal the waste in an airtight envelope. The sealed chambers are equipped with wells to remove the biogas naturally produced by the break down of organic matters.
The biogas collection network connects the wells in each chamber to remove the biogas produced by the break down of the organic matters. A booster compressor then sends the biogas to the WAGABOX® upgrading unit.
The flare stack may be used to burn off the biogas should the WAGABOX® unit be unable to upgrade the biogas (e.g. during maintenance operations), to avoid any methane emissions into the atmosphere.
The raw biogas delivered to the WAGABOX® unit contains methane, carbon dioxide and air (oxygen and nitrogen), and is often heavy with moisture. It also contains traces of other gases, particularly hydrogen sulfide and volatile organic compounds (VOCs). The raw biogas needs to be pretreated before starting methane separation.
Before upgrading biogas, the hydrogen sulfide content has to be removed using activated carbon to prevent this toxic and corrosive compound from damaging any equipment. The biogas is then cooled in a heat exchanger to remove the water through condensation.
The pressure swing adsorption system, or PSA, removes the volatile organic compounds present in the biogas. It comprises three vessels mounted side-by-side which contain different adsorber beds.
The oil removal system, or ORS, removes any traces of oil mist left by the compressor to protect the upgrading membranes from damage.
The membrane upgrading module consists of a compressor and sets of membranes, all installed inside a container. The unit separates the carbon dioxide from the other components. The container also houses other equipment: controllers that operate the installation, control valves and another compressor which sends the biomethane to the injection station.
The pressure and temperature swing adsorption system, or PTSA, removes any residual traces of carbon dioxide from the biogas before cryogenic distillation to prevent “dry ice” from being formed. The PTSA consists of two vessels which contain microporous adsorbents and operate alternately: when one vessel is in the adsorption phase, the other is regenerating.
The cryogenic distillation unit separates the methane from the nitrogen and oxygen contained in the biogas. It consists of a distillation column and a heat exchanger. A small amount of liquid nitrogen is used, particularly during the start-up phase. The biogas is cooled to -161°C (112K) to liquefy the methane, which is recovered through gravity, whereas air gases are sent to the oxidizer.
The thermal oxidizer is used to burn off the different gas flows generated by the landfill gas upgrading process (particularly those containing VOCs) to prevent the emission of pollutants into the atmosphere.
The electrical room houses the control system, the electrical cabinets, the telecom rack and other equipment. Entirely automated, the WAGABOX® unit operates autonomously 24/7 and is remotely monitored by Waga Energy team.
At the end of the upgrading process, the methane is 98% pure: landfill gas has become Renewable Natural Gas (also called “biomethane”). RNG is transported to the grid operator’s injection station.
The injection station is the entry point to the grid of the natural gas grid operator. The station contains equipment for checking the compliance of the Renewable Natural Gas with injection requirements, odorizing the gas to help detect leaks should they occur, and measuring the volume injected.